As a reminder, the recently approved National Motor Freight Classification (NMFC) freight classification changes went into effect this weekend (August 5th, 2017). These changes will have far-reaching effects on LTL shipments of certain commodities in the NMFC that are based on density ratings, such as Plastic or Rubber Articles, Expanded, NOI (157320), and others. Previously, most items assigned a class based on density were subject to one of two tables. The so-called 9-tier classification broke down density into 9 sub ratings as follows:
Sub 1 |
Less than 1 |
400 |
Sub 2 |
1 but less than 2 |
300 |
Sub 3 |
2 but less than 4 |
250 |
Sub 4 |
4 but less than 6 |
150 |
Sub 5 |
6 but less than 8 |
125 |
Sub 6 |
8 but less than 10 |
100 |
Sub 7 |
10 but less than 12 |
92.5 |
Sub 8 |
12 but less than 15 |
85 |
Sub 9 |
15 or greater |
70 |
The 11-tier classification contained 11 density breakdowns:
Sub 1 |
Less than 1 |
400 |
Sub 2 |
1 but less than 2 |
300 |
Sub 3 |
2 but less than 4 |
250 |
Sub 4 |
4 but less than 6 |
150 |
Sub 5 |
6 but less than 8 |
125 |
Sub 6 |
8 but less than 10 |
100 |
Sub 7 |
10 but less than 12 |
92.5 |
Sub 8 |
12 but less than 15 |
85 |
Sub 9 |
15 but less than 22.5 |
70 |
Sub 10 |
22.5 but less than 30 |
65 |
Sub 11 |
30 or greater |
60 |
Effective August 5th, the 9-tier breakdown will go away and NMFC items subject to it will be replaced by the 11 tier breakdown. This change is actually good news for shippers, as it provides for a lower class for shipments that are very dense, specifically over 22.5 lbs per cubic foot. The other change however is not so favorable. The 11-tier breakdown will change the sub 4 rating for articles that have a density of 4 but less than 6 pounds per cubic foot. Previously this was rated as a class 150, but will now be rated at a class 175:
For shippers whose LTL shipments were previously rated at class 150 based on density and will now be rated at class 175, this represents about a 15% increase in freight rates. For shippers with an FAK rating of 150, this should not change that rating, but items that were previously in the actual class range may now change. For example, if a shipper has a FAK class 100 rating on items with an actual class of 100-150, and they ship Plastic Articles with a density of 4-6 pcf, this shipment will no longer be subject to the FAK class 100 and will instead move at the actual class of 175.
Please contact your Logistics Plus North American Division (NAD) freight representative if you have any questions regarding the new rules.
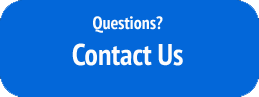