by logisticsplus | Jul 5, 2022 | News
FOR IMMEDIATE RELEASE
Logistics Plus Acquires Concord-Trans to Expand its Ukraine Operations
The acquisition offers additional freight forwarding and project cargo capabilities to the region.
ERIE, PA (July 5, 2022) – Logistics Plus, Inc. (LP), a leading worldwide provider of transportation, logistics, and supply chain solutions, has announced the acquisition of Concord-Trans, a Ukrainian-based freight forwarding and logistics company. Located in Ukraine’s capital city, Kyiv, with a second office in Odesa, the purchase includes nearly a dozen in-country logistics professionals specializing in road, sea, and air freight transportation, customs clearance capabilities, and project cargo management.
“Logistics Plus remains committed to supporting Ukraine, and the Ukrainian people whose lives have been ripped apart by this war,” said Yuriy Ostapyak, COO for Logistics Plus and a Ukraine-born U.S. citizen. “The activities needed to rebuild Ukraine after the war will be significant. The acquisition of Concord-Trans gives Logistics Plus the additional in-country expertise required to play a major role in providing the logistics solutions needed to support the long-term rebuilding efforts.”
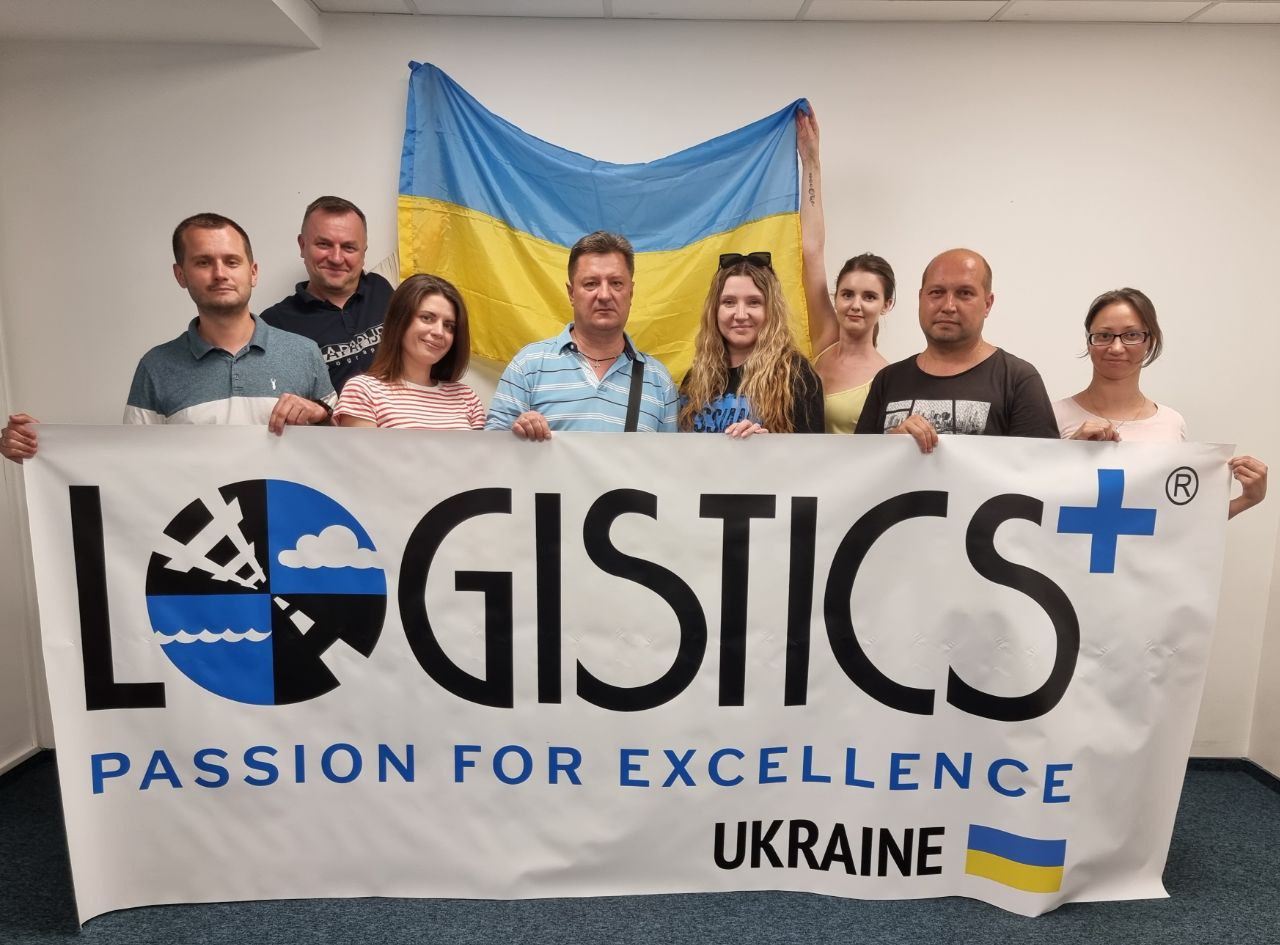
The LP Ukraine Kyiv Team
“We are very pleased to join the Logistics Plus team,” said Oleksandr Korzun, General Manager for Logistics Plus Ukraine. “It is especially nice to do this at such a difficult time for our country. I am very grateful to Logistics Plus for the outstretched hand of help to our company and Ukraine as a whole. I hope that together we will do a lot of good for both the company and Ukraine.”
Before the acquisition of Concord-Trans, Logistics Plus already had a significant presence in Ukraine, with an office of nearly fifty people located in Ivano-Frankivsk, a city of about 240,000 people in the western portion of that country. Earlier this year, Logistics Plus established lpukrainerelief.com, which has raised over $660 thousand to help Ukrainian refugees. The company has also been actively working with local organizations to warehouse and transport multiple containers of relief goods to the region.
To learn more about the expanded “LP Ukraine” office and capabilities, please visit www.logisticsplus.com/meet-the-logistics-plus-ukraine-team.
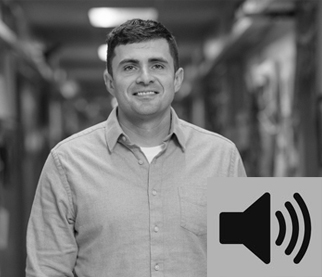
90-second audio clip
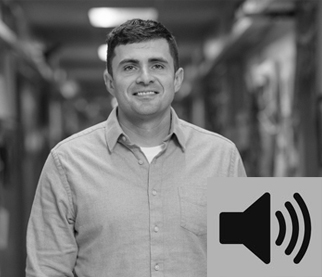
60-second Audio Clip
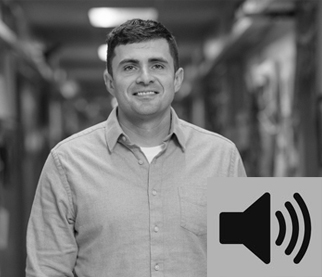
30-second Audio Clip
About Logistics Plus Inc.
Logistics Plus, Inc. is a 21st-century logistics company that provides freight transportation, warehousing, fulfillment, global logistics, business intelligence, and supply chain management solutions through a worldwide network of talented and caring professionals. The company was founded 25 years ago in Erie, PA, by Jim Berlin. Today, Logistics Plus is a highly regarded, fast-growing, and award-winning transportation and logistics company. With its trademark Passion For Excellence™, Logistics Plus employees put the ‘plus’ in logistics by doing the big things properly, plus the countless little things that ensure complete customer satisfaction and success.
The Logistics Plus® network includes offices, warehouses, and agents located in Erie, PA; Aurora, CO; Buffalo, NY; Charlotte, NC; Chicago, IL; Chino, CA; Cincinnati, OH; Cleveland, OH; Colton, CA; Dallas, TX; Dayton, NJ; Des Moines, IA; Haslet TX; Houston, TX; Laredo, TX; Lexington, NC; Los Angeles, CA; Miami, FL; New York, NY; Olean, NY; Ontario, CA; Phoenix, AZ; San Francisco, CA; Tulsa, OK; Vancouver, WA; Australia; Belgium; Brazil; Canada; China; Colombia; Czech Republic; Egypt; France; Germany; India; Indonesia; Japan; Kazakhstan; Kenya; Libya; Malaysia; Mexico; Netherlands; Poland; Saudi Arabia; Singapore; Taiwan; Turkey; UAE; Uganda; and Vietnam; with additional agents around the world. For more information, visit www.logisticsplus.com or follow @LogisticsPlus on Twitter.
Media Contact:
Scott G. Frederick
Vice President, Marketing
and LTL Carrier Relations
Logistics Plus, Inc.
(814) 240-6881
scott.frederick@logisticsplus.com
Click the image below to download the Logistics Plus logo:
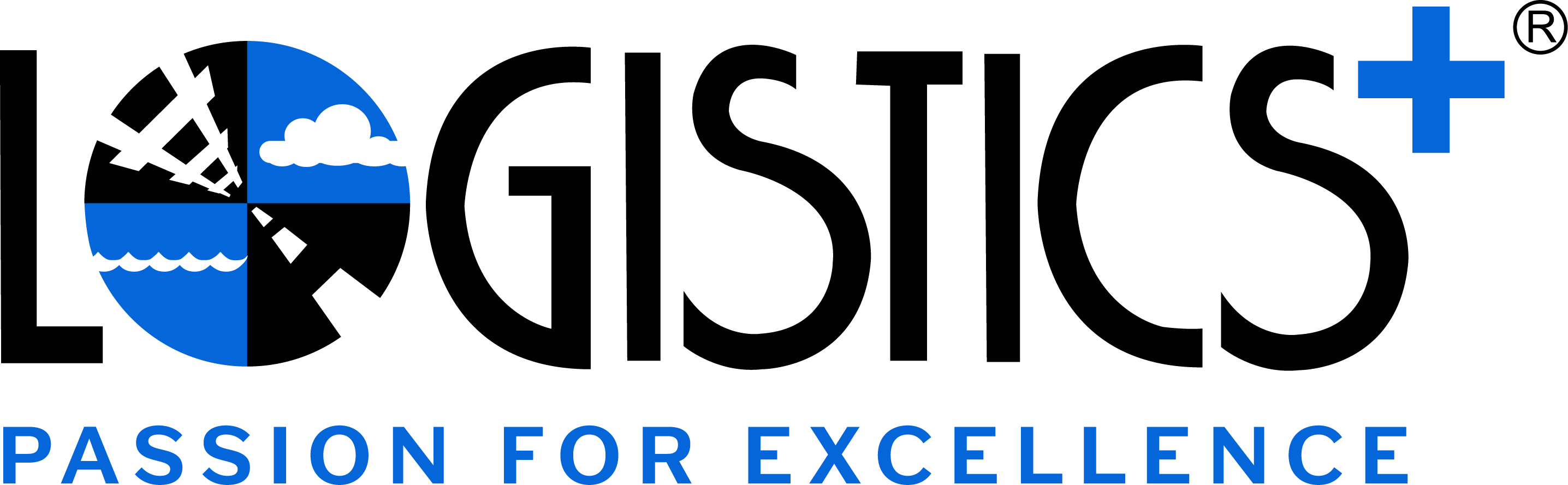
by logisticsplus | Jul 1, 2022 | News
Logistics Plus Ukraine (aka LP Ukraine) is expanding its presence with new offices in Kyiv and Odesa (joining our existing Ivano-Frankivsk office). Logistics Plus added the new offices to its growing global network through the acquisition of Concord-Trans, a successful Ukrainian-based freight forwarder. Some of the primary logistics services offered by this new team include:
- Imports and Exports
- Airfreight
- Ocean freight
- Customs and compliance
- Project cargo
- DOD and Military cargo
- Installations
- Consulting
LP Ukraine General Manager Oleksandr Korzun shared his excitement about joining the Logistics Plus team. “We are very pleased to join the Logistics Plus team. It is especially nice at such a difficult time for our country. I am very grateful to Logistics Plus for the outstretched hand of help to our employees and Ukraine as a whole. I hope that together with the Logistics Plus team, we will do a lot of good for both the company and Ukraine. Together to victory! Glory to Logistics Plus! Glory to Ukraine!”
Meet The Team
Oleksandr Korzun – General Manager
oleksandr.korzun@logisticsplus.com
Phone: +38-067-220-0029
Andrii Krutyi – Commercial Director
andrii.krutyi@logisticsplus.com
Phone: +38-063-952-5899
Victoria Gribova – Air & Sea Freight Manager
victoria.gribova@logisticsplus.com
Phone: +38-063-149-1433
Oksana Onoprienko– FEA Manager
oksana.onoprienko@logisticsplus.com
Phone: +38-063-149-1433

For any requests involving the Ukraine team, please email ukraine@logisticsplus.com. We thank you for all current business and future opportunities, and we look forward to assisting you.
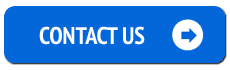
by logisticsplus | Jun 28, 2022 | News
FOR IMMEDIATE RELEASE
Logistics Plus Recognized with Another Top Supply Chain Project Award
It’s the fourth straight year and the sixth time that Logistics Plus has been recognized by Supply & Demand Chain Executive for a top supply chain project.
ERIE, PA (June 28, 2022) – Logistics Plus, Inc. (LP), a leading worldwide provider of transportation, logistics, and supply chain solutions, is proud to announce it has been selected by Supply & Demand Chain Executive, an industry-leading publication covering the entire global supply chain, as a recipient of a Top Supply Chain Projects Award for 2022. Logistics Plus has been honored for managing a top global supply chain project for a fourth consecutive year and the sixth time in the past seven years.
The Top Supply Chain Projects Award (formerly known as the SDCE 100) spotlights successful and innovative transformation projects that deliver bottom-line value to small, medium, and large enterprises across various supply chain functions. These projects show how supply chain solution and service providers help their customers and clients achieve supply chain excellence and prepare their supply chains for success.
The supply chain project submitted by Logistics Plus that earned this year’s recognition was a Covid-19 test kit project. In late December 2021, the Biden administration announced a new initiative to supply free Covid test kits to all Americans. Shortly after, a top supplier in the medical device industry contacted Logistics Plus to assist with importing, sorting, and distributing large freight shipments of the test kits. Within days of the request, Logistics Plus was able to acquire a large warehouse within miles of O’Hare airport in Chicago. The LP team managed the air charter imports, sent TSA drivers on-site to pick up the freight, and brought the PMCs (airline pallets) to its warehouse. From there, Logistics Plus broke down the PMCs, sorted the cartons, and received them into its warehouse management system (WMS). The final piece of the puzzle was to group, palletize, and shrink-wrap the test kits on standard pallets in preparation for outbound distribution across the United States.
“This project was a perfect example of the fluidity and speed of our company,” said Jim Berlin, Founder and CEO of Logistics Plus. “Within days of the request, our team received pallets and prepared outbound orders. It was truly a team effort during a time of need. Thank you to Supply & Demand Chain Executive for recognizing this Herculean effort with a top supply chain award.”
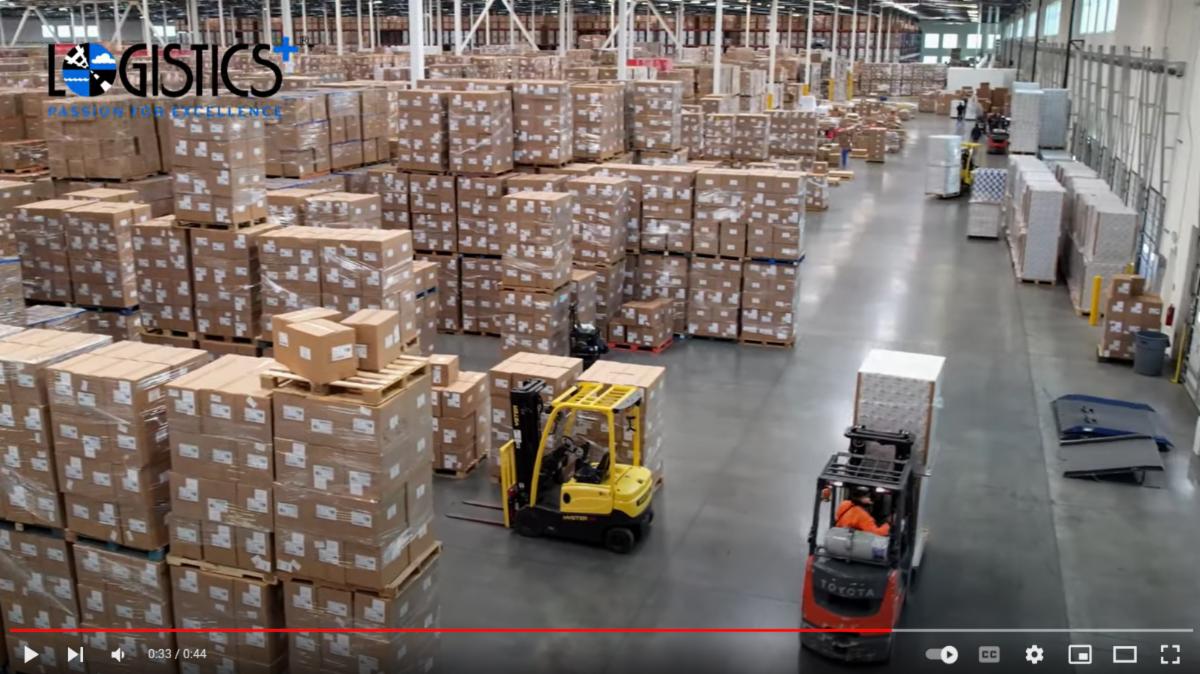
Watch the video above to view an example of COVID Test Kit Project being managed at the Logistics Plus warehouse in Chino, CA.

About Supply & Demand Chain Executive
Supply & Demand Chain Executive is the only supply chain publication covering the entire global supply chain, focusing on trucking, warehousing, packaging, procurement, risk management, professional development, and more. Learn more at www.SDCExec.com.
About Logistics Plus Inc.
Logistics Plus, Inc. is a 21st-century logistics company that provides freight transportation, warehousing, fulfillment, global logistics, business intelligence, and supply chain management solutions through a worldwide network of talented and caring professionals. The company was founded 25 years ago in Erie, PA, by Jim Berlin. Today, Logistics Plus is a highly regarded, fast-growing, and award-winning transportation and logistics company. With its trademark Passion For Excellence™, Logistics Plus employees put the ‘plus’ in logistics by doing the big things properly, plus the countless little things that ensure complete customer satisfaction and success.
The Logistics Plus® network includes offices, warehouses, and agents located in Erie, PA; Aurora, CO; Buffalo, NY; Charlotte, NC; Chicago, IL; Chino, CA; Cincinnati, OH; Cleveland, OH; Colton, CA; Dallas, TX; Dayton, NJ; Des Moines, IA; Haslet TX; Houston, TX; Laredo, TX; Lexington, NC; Los Angeles, CA; Miami, FL; New York, NY; Olean, NY; Ontario, CA; Phoenix, AZ; San Francisco, CA; Tulsa, OK; Vancouver, WA; Australia; Belgium; Brazil; Canada; China; Colombia; Czech Republic; Egypt; France; Germany; India; Indonesia; Japan; Kazakhstan; Kenya; Libya; Malaysia; Mexico; Netherlands; Poland; Saudi Arabia; Singapore; Taiwan; Turkey; UAE; Uganda; and Vietnam; with additional agents around the world. For more information, visit www.logisticsplus.com or follow @LogisticsPlus on Twitter.
Media Contact:
Scott G. Frederick
Vice President, Marketing
and LTL Carrier Relations
Logistics Plus, Inc.
(814) 240-6881
scott.frederick@logisticsplus.com
Click the image below to download the Logistics Plus logo:
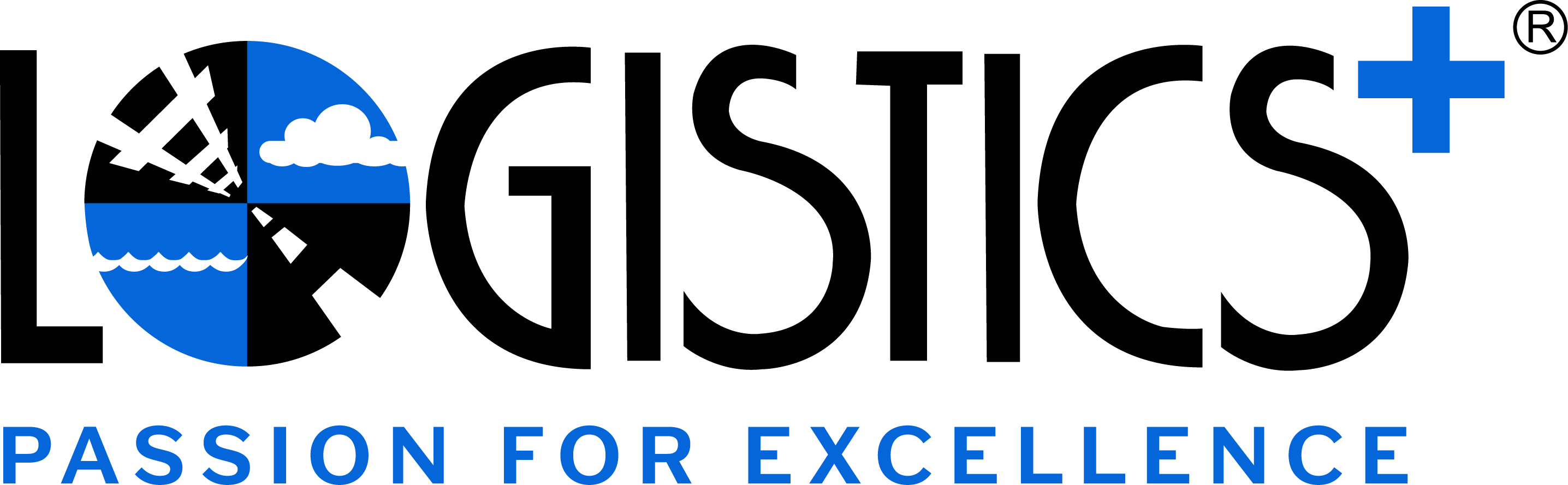
by logisticsplus | Jun 24, 2022 | News
Dennis Melgert, Vice President of the Logistics Plus Chemicals Division, was featured on the weekly Business Spotlight program from WPSE AM 1450/FM 107.1 Radio. Business Spotlight is a 30-minute program airing Fridays at noon. Each segment focuses on a business or organization that is making an impact across the region.
In this segment, Dennis discusses his background, his path to joining Logistics Plus, the company’s chemical division, company culture, and more. You can listen to a replay of the interview on the Logistics Plus Podcasts page or by clicking the audio link below.
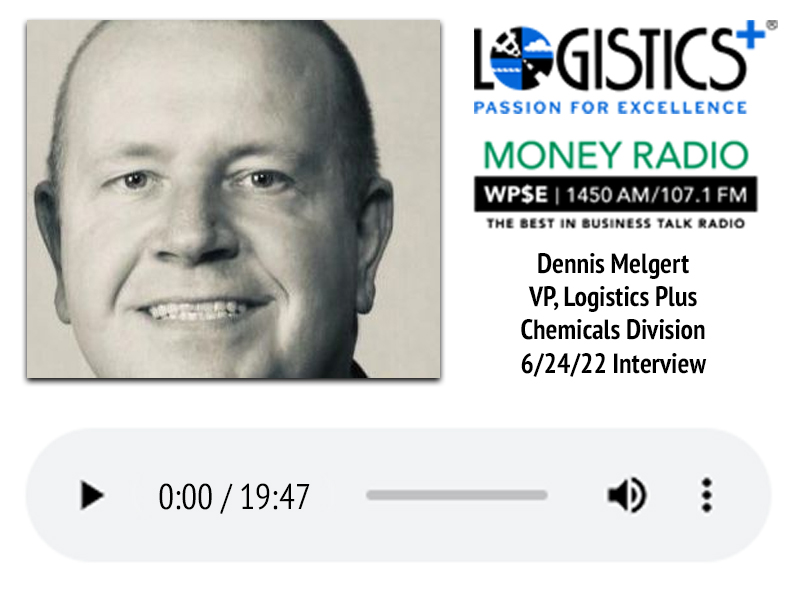
by logisticsplus | Jun 20, 2022 | News
Logistics Plus COO Yuriy Ostapyak was interviewed and featured on the latest episode of the Inbound Logistics Podcast titled “War in Ukraine: How is One 3PL Navigating the Ultimate Disruption?”
Moving out of the pandemic is one thing, but how would your business respond if it then moved into a war zone? What balance of technology, communications, and partnerships are crucial to keeping your supply chain going in that kind of conflict? Yuriy Ostapyak, a Ukrainian-born U.S citizen, shares his perspective on the war in Ukraine and how Logistic Plus continues to operate and support Ukrainian refugees.
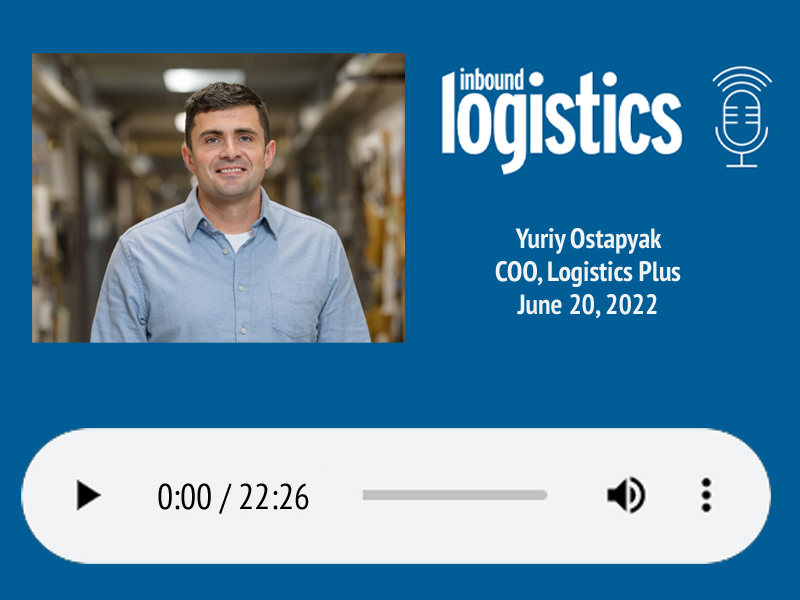

Listen to this and other Logistics Plus Podcasts & Interviews on the Logistics Plus website under About>Media & Resources.
by logisticsplus | Jun 14, 2022 | News
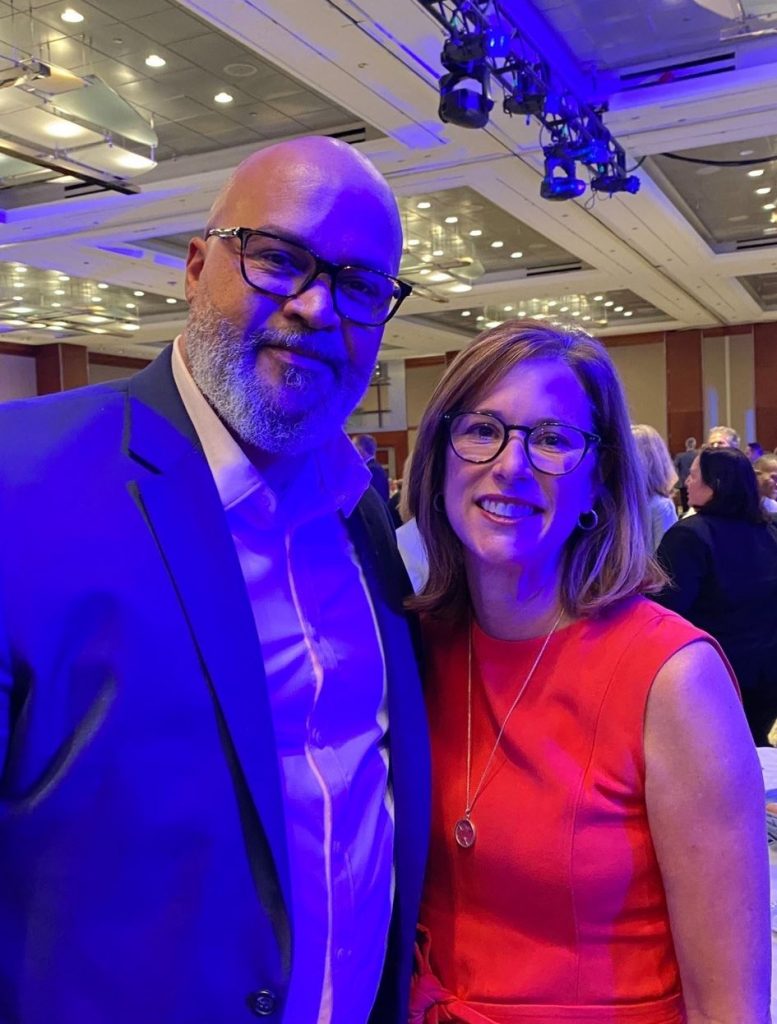
(Shane Gross with Karen Sauder)
Logistics Plus VP of Global Strategic Partnerships Shane Gross attended the Chicagoland Chamber of Commerce 118th Annual Meeting last week. This year, the Chamber had Google President of Global Clients and Agency Solutions Karen Sauder as their keynote speaker.
At this year’s annual event, the Chicagoland Chamber announced the findings of the Chicago Tech Effect, a comprehensive analysis of the city’s tech ecosystem, and the priorities needed to help maintain Chicago’s place as a global technology hub. Some of the findings included:
- Chicago is one of America’s leading tech hubs, with 18% growth in the tech workforce over the last decade
- Widespread tech growth in Chicago is fueling upward mobility and greater economic equality
- Chicago outperforms national averages for diversity in technology
About the Annual Meeting
The Chicagoland Chamber of Commerce assembles more than 700 business and civic leaders of Chicago for the Annual Meeting of Membership. We invite Chicago’s business community to join us at this event, the premier business event for Chicagoland to celebrate the contributions commerce and industry make to a great city.
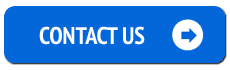